Update Feb 20th
The next sentence (still under suggestion number 2) said: It will also be easier to attached the nose to the shell if a piece of scrap brass is cut to the shape of the back of the nose casting, soldered to the shell and then screwed to the back of the nose casting.
I have not been looking forward to this point of the build. The problem is LWS messed up the upper corner bends on the engineer’s side of the shell. I have never build a brass locomotive kit but I can tell you this square roof bend did not match either the round end cap or the round nose casting. You will need to work real hard to un-bend that shells square corner… while at the same time holding the shell in place with clamps… while at the same time securing the rear end cap to the shell with clamps… while at the same time making sure all these parts don’t fall off the bench.

I have read in other forum threads that soldering brass was like an art form, the more your practice the better you will get. That is a true statement and see lots of forum members who are absolute artists in soldering brass. I tried it… I’m not one of those guys. All during this building adventure I have been desperately practicing my solder skills on the brass fuel tank pieces that came with the kit. Even with practice my brass solder connections looked awful and just too embarrassing to post on this forum.
I’m nervous to admit it but instead of soldering I attempted using CA glue as recommend back in that Feb 1978 OSR issue. From K&S metals I purchase a 3/16” brass right angle (part #9881) that was 12” long to help with the shells assembly. This right angle brass was cut into ½” brackets, sanded and tacked on with CA glue to the locomotives rear end piece. Also, right angle brackets were sanded and placed inside the shells inside front edge where it will meet with the brass nose casting. Fail.
I quickly found out CA glue does not hold on to large structural brass components. Apparently, CA glue is only meant to hold non-structural components or very small brass details. So, I tried again, this time epoxy was used as recommended back in OSR issue #54. Fail again. I found out epoxy is too brittle for this type application and rear end cap broke off the shell with a small amount of pressure.
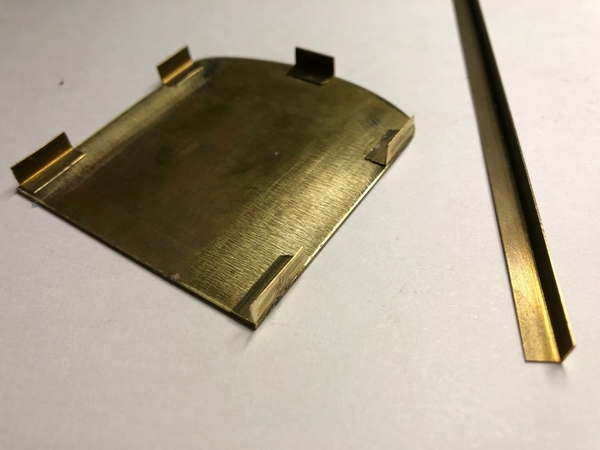

Okay at this point, this LWS E9 kit was either going back into its original box to live a lonely life as a 4-pound doorstop or I had to learn how to solder brass. Searching on YouTube I found a 10-minute video called “Soldering for Scale Modelers”. After watching this instructional how-to video I gave the shell another attempt using my tools.
I pulled out a soldering station my son gave me, can of Weller tip tinner, can of Weller rosin flux paste, roll of 60/40 solder and then scrubbed with sand paper and cleaned the glue off the shell’s inside walls. I followed that video’s instructions but just couldn’t get enough heat to both brass sides at the same time for my solder to flow smoothly. I realized at this point the person in that video was working with much thinner brass sheets and the tip on my solder iron was much too small for this kind of work. Sure, a couple solder globs were holding in a few places inside the shell but it looked like chewed-up bubble gum.
Next, I pulled out my old soldering gun with a flat tip and tried again. Nope, still not enough uniform heat to the shell’s brass joints. I just don’t have the right tools for this job.
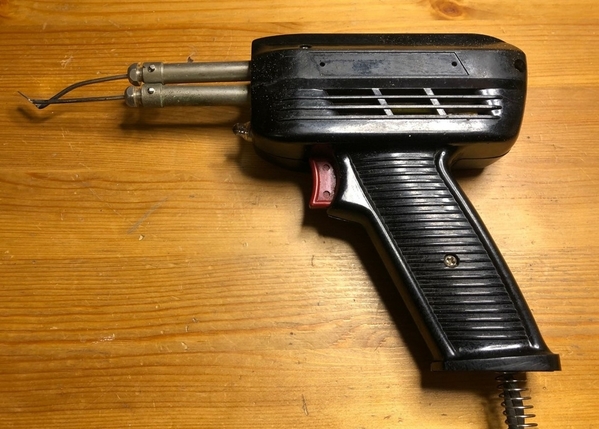
Then I re-read what @bob2 said above in the post about using a flame. So, I drove down to the hardware store and purchased a micro torch and can of butane. A quick hit with the micro torch inside the brass shell and the problem was solved! Thank you @bob2 for the solid advice, you saved this project.

Guys, I’m not going to get everything right on my first brass kit but I’m trying (and sharing what not to do). I’ll continue to practice on the fuel tank with my soldering iron. It's clear now my next purchase needs to be an assortment of larger tips for the soldering iron.
Stay tuned for the next update…