It's Monday, so I'm back to work. I use that term loosely.
Got the positioning of the pavement and roadway finalized and measured parallel to the layout's sides.
I measured the pavement from the layout edges so it was parallel to them. I marked the layout base to be able to put it back correctly. I located each building roughly on the pavement, and then, off the layout, laid in some perpendicular lines from the pavement edge. I held each building over its location and marked the x-y position of where the power leads will drop through. I drilled the holes in the styene on the drill press, and after positioning the pavement back on the layout, using those holes as a drill jig, drilled the holes through the layout. To drill through the plastic I use a drill sharpened to a 90° plastric-drilling and for the Masonite I used a spur bit.
In n-scale a 3-lane road (33 scale feet) is roughly 2.5". I using that number. I'm having two driving lanes and one for parking with each lane 11 scale feet. I'm making the roadway out of thick water-color painting paper. In this way I can use water-based paint without the fear of the paper curling up too badly. I laid out the paper old school using compass, straight edge, paper cutter, scissors and a pencil. Long cuts were made on the paper cutter. Curves and trims were done with #11 blade. After trimming I temporarily held the sections together with Scotch Magic Tape.
I needed to do some minor excavation around the back road perimeter to remove a little bit more of the Sculpt-a-mold so the road would sit flat on the layout surface.
After taping the long pieces together and fitting in the ends, I used a compass to swing the corner radii to make a 'steerable' turn for the tiny n-gauge cars.
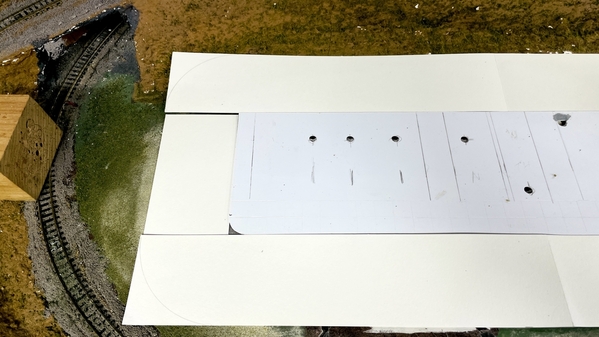
I first freehand cut these with the #11, but realized it would be easier with a scissors. After cutting the corners and taping them to the rest of the road, I cut some small filler pieces to complete the road around the corners.
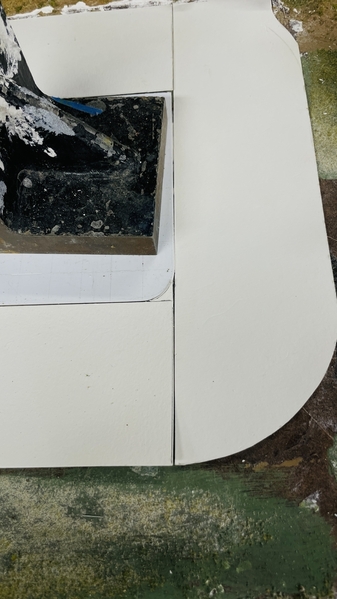
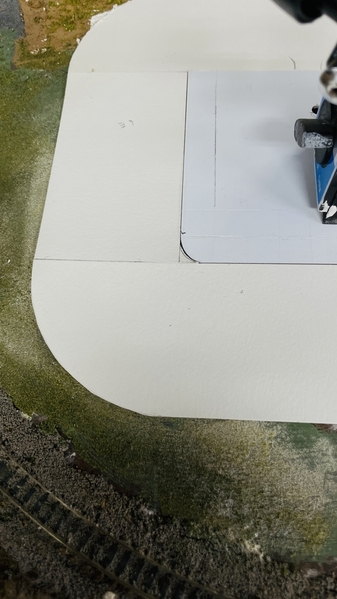
There was one area left that needed a lot of fiddling. The kids had some up with the idea to have a tunnel under the mainline, but it couldn't exit because there was a lower level track behind it. So we did a "Roadrunner" bit with a flat wall painted like a tunnel. I didn't change this for this new application. But the street needed to go into it and it was at right angles. I had to custom fit the paper road into this space.
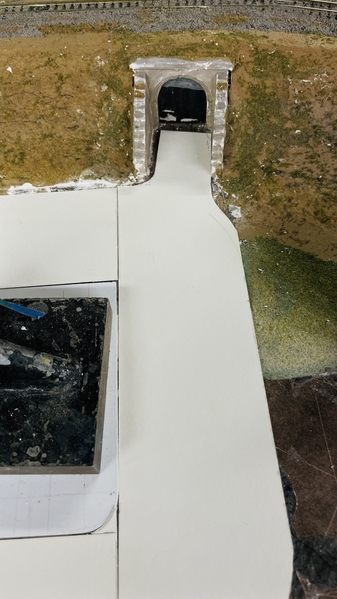
Here's the road fit up for the next operation.

While I haven't finalized just what kind of adhesive I'm going to use to hold all of this in place—I'm leaning towards the 3M Transfer Adhesive Tape—I needed to seal the sub-surface so it was a good surface for the adhesive. I used this. It's a very good water-based sealer that dries quickly and cleans up with water.
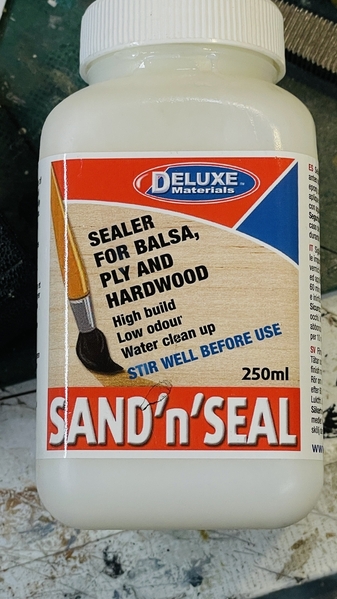
And this is the surface prepared for attaching the pavement/base and roadway. It was still wet when I took this.

I'm going to airbrush the pavement a concrete color, gloss coat it, put on an aging wash to bring out the sidewalk expansion grooves, and then Dullcoat it.
For the road, I marked the road line locations, but not sure which approach to take: paint it all asphalt-color and then add thin white/yellow tape to simulate the lines, OR paint the line areas on the bare paper, lay the thin masks down and paint the asphalt color and then remove the tape to expose the road lines. I've done it both ways, but lean towards the latter. I means redoing all the layout I did since it will be painted black. Either way, I will be doing this tomorrow.
Oh... one more thing. I found that the point where the train derails randomly... the track gauge was just a skosh tight. A little filing on the inner surface of the rail with gap repair and the train slides through without a hitch. I think I've finally got it.