Power on a MTH • TMCC • LionChief Plus Layout & Conventional Operations.
This is how I manage 4 Lionel, 180 Watt Powerhouse Bricks on my layout. It is impossible to get 18.0 Volts to your rails with a 180 Watt Lionel Brick. The only way you could get 18.0 Volts to the track, would be to cut off the mail plugs on the Lionel Brick and run the wire directly to the track. If you cut off the male plugs, this will void the Lionel Warranty. According to Lionel, these Lionel Power House Bricks must be plugged into a ZW.
I use tubular track and each main line has about 100 feet of track, for a total of 400 feet.
How the power gets to the rails on my layout. from the starting point.
1. Starts at the homes power panel in the train room. Leaves on a dedicated 15 amp circuit. This line is also GFI. The panel also has a whole house surge protector.
2. Enters the layouts control panel and enters a Kill Lighted Switch.
3. Than the power goes to a junction box with 4 plugs, the outlet than breaks out into 4 power Surge / Arrest Protectors. Everything on the layout is plug into these strips with space left over.
4. The power now enters 4 Lionel 180 Watt Powerhouse Bricks, on the end of each Lionel Brick is a male plug. These 4 male plugs are plug into the back of a Lionel ZW Transformer.
5. The power leaves the ZW on 14 Gauge Stranded Wire. Next it goes to the MTH / TIU. There are 4 throttles - Left to right on the ZW - Track 4 / Track 3 / Track 2 / Track 1.
6. The wire is attached to the Track Interface Unit on the Input Side with, Klein / Ideal Terminal Connectors. Track 4 to = Fixed Voltage, Track 3 to = Variable Voltage, Track 2 to = Variable Voltage, Track 1 to = Fixed Voltage. This means that the large throttles on the ZW are fixed and the small inter throttles on the ZW are variable voltage.
7. The power leaves the Track Interface Unit on the Out Put side and goes to several MTH 50-10-1020 24-Port Terminal Blocks, This block sends the current to the layout control panel that sends the power to the tracks and sidings, using single pole, single throw switches.
8 - Each main line has 3 blocks so I can run conventional locos, using the throttles on on the Lionel ZW. Old school operations. The 14 gauge wire is solder to the track about every 6 feet to the inside of the rails.
9 - The Lionel TMCC is wired to the TIU with a MTH cable 50-1032 and a 14 gauge ground wire.
Below are two wiring diagrams (1) My Layout (2) Wiring diagram from the MTH • DCS Operator's Manual, Fifth Edition, Page 11. Note: I also use the "OGR Video Guide, Digital Command System".
Any questions or a suggestions for a do over. Gary / (Click on diagrams to enlarge).


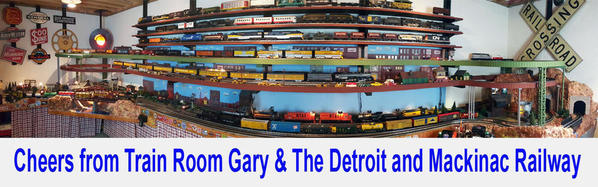