My best track tool is a pair of Small Nipper Pliers shown below. Mine are from a cheap Chinese pliers set (Harbor Freight now days) and are small, about 4" long.
I use these to tighten up the rail pins inside the rails. and to tightly wrap the piece of shim or flashing stock around the pin in the gap. I usually cut a strip of flashing about 3/8" wide and a few inches long. Then I use a small tin snips to cut a piece about the width of the gap and it will be 3/8" long. I cut it too wide and then keep trimming it down until it fits in the gap. I then wrap it around the pin in the gap with my fingers and squeeze it tight with the nipper pliers. If 3/8 " is to long I just let it hang down. It should take only a minute or two do each gap.

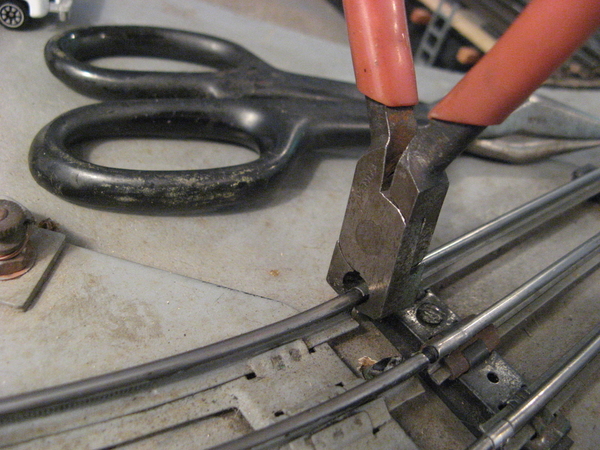
This will not work with the gap from the tooth picks I use mostly used for insulated center rail gaps. (I know Lionel makes plastic pins for this use but I did not have them years ago.) Note the picture above has a Lionel plastic pin in the center rail. I have lots of insulated center rails as my whole layout is blocked into 5 or so foot sections.
I cut a gap sized of plastic insulation from some solid electrical wire to fill the gap. I split the little do nut of insulation with a X-acto knife and slip it on.
Another useful homemade tool is a Track Cutting Jig.
Track Cutting Jig
Early on I made a Track Cutting Jig to help cut short sections of straight 027 track.
It is made from a scrap of 3/4" wood, size 2" x 2 1/4 " with a same size 3/8" plywood glued on the bottom. Three slots were sawed, with a band saw, 1/4" deep and 1/8" wide at the spacing of the three rails of 027 track. A 1/16" wide slot was cut at 90 degrees to the track slots to accommodate a hack saw blade.
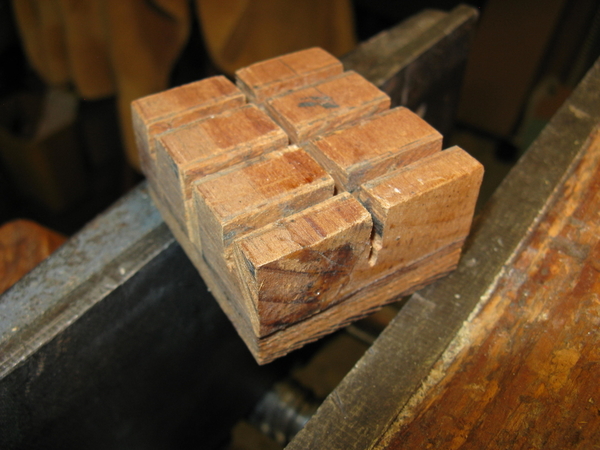
A piece of 1/2" plywood was made to act as a Track Hold Down. Shown at the top of picture. Groove was cut to go over the track tie if necessary
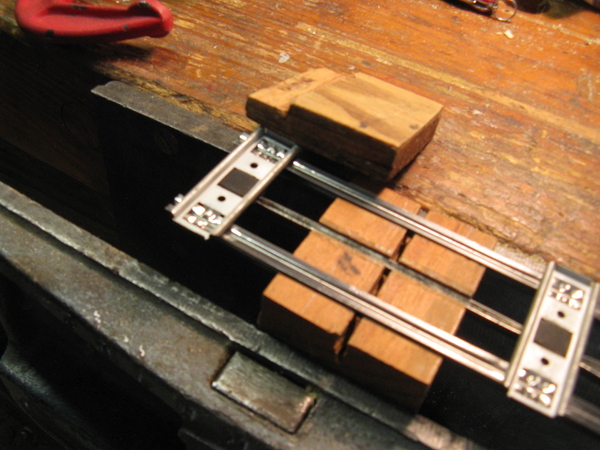
Picture of clamp holding Track Cutting Jig, track to be cut with hack saw and Track Hold Down. The Track Cutting Jig is held in vise.
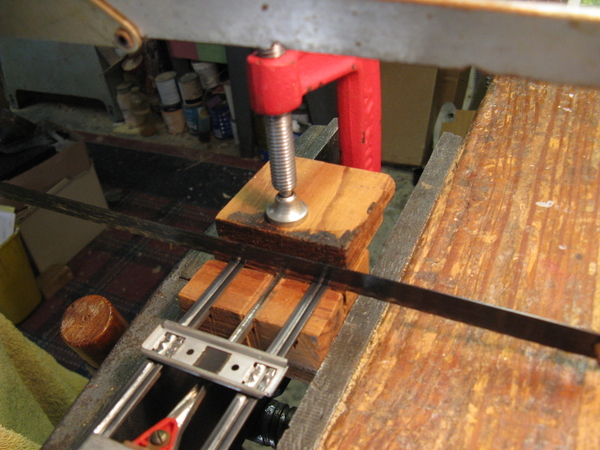
I use a fine tooth hack saw blade and find the Track Cutting Jig makes cutting shorter pieces of track an easy, neat job.
Both of these track tools were reported in my layout building post, in post 53 b, linked below:
https://ogrforum.ogaugerr.com/...08#79142442664029608
Charlie