OK- I'll weigh in. Not that I am RIGHT, or that anybody really cares, but...
All of the aforementioned ways to build benchwork do a good job. As for me- I have done FIVE layouts: #1 a standard 2X4 frame/ cross member w/ 5/8" plywood top, HO scale, assembled w/ drywall screws, and using the "cookiecutter" method to make grades. It never ran, because my family needed the 1/4 of a basement train room before my trains could run = teardown #1.
Tear down #2 was a "shelf-style" HO switching layout at one end of the laundry / utility room. Plywood framed in 2X4, and mounted to the block walls mounted to block using shelf brackets. Never ran. We moved.
# 3 was 1/2 of a basement plus 2 feet. Built using the Westcott L-Girder method. Never ran, after a year+ of work on the benchwork, I started on the sub-roadbed- right before the divorce.
#4 was in my new bachelor condo- another HO layout. Completed the benchwork, AND the sub-roadbed, as well as the Homosote. I was getting pretty good at it, but the trackwork - I just could never get it right. Wobble wobble down the track, then derail.
Here is what I have learned:
1. Time- working on trains needs something around a 2-3 hour window minimum- 45 minutes to figure out where you left off three weeks earlier, 2 hours of work, and the rest before bed is cleanup.
2. Difficulty- it is not really difficult, but what is easiest is to get all tied up in details, and never have trains running, no fun. Unless your real hobby is crappy woodworking.
3. Wood- it is hard to find decent, straight lumber. So, you either have to buy "cabinet grade" wood, or pick through the junk at a big box store, then quickly cover it up so your visitors don't think you used old pallets.
4. HO- "fiddly". Your bench-work, roadbed, and track-work better be top rate- or you have a crummy running layout.
SO: for layout #5: I decided I wanted Lionel and O Gauge. They run. They run most of the time. They can be worked on using 70 year old eyes. I decided I didn't want to be a crummy woodworker. I also decided I wanted to use pre-made commercial track w/ roadbed (vs. "flex track"), and chose FasTrack.
I had the hobby shop draw up a track plan (the plan is least important part IMO- ANY decent track plan, that fits your space, is a good one.) They ALL will be boring eventually and what is fun becomes scenery, buildings, etc. anyway.
I sent the track plan to Matt Hewitt, Benchridge Benchworks. https://www.benchridge.com/
He designed a set of modular tables, most of them 2' X 4' size, bolted together using 5/16" cap screws, with reinforced leg sets made of 2 X 2 legs, then the leg sets braced w/ 3/4 " masonite, glued and screwed. All wood filled and sanded. And he cuts his own wood, so it's straight, even pretty. Of 26 sets of legs- TWO had to be re-leveled when set up. 1/2" flat tops. A 12 X 20 set of tables- delivered, and set up in 3-1/2 hours for a 12 x 20 layout. Trains were running within 3 weeks. Cost was equal to a commercial modular table, BUT I didn't have to assemble it- Matt did.
I am too old for carpentry!!
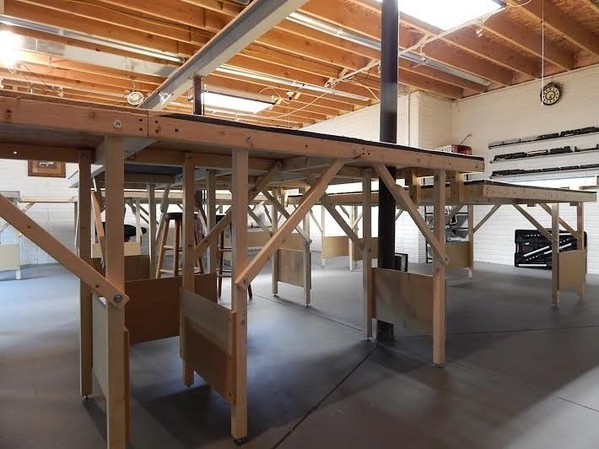
