Witzinger's Post 6 – September 4, 2021
I chose Witzinger’s as a model for my layout expansion scene because I needed a background building and because it had a rooftop billboard that would be noticed even though it would be at the rear of the layout.
As packaged in the Bar Mills kit, the billboard was printed on paper and had to be attached to a rectangular backing piece and then to a framework, as shown in Photo 57. I applied a mixture of alcohol and India ink to give the wood parts a weathered look, as I did to the other wood parts that I added to the billboard framework. The backing piece had “peel-and-stick” adhesive on its front, so I simply removed the protective covering (peel) and pressed the printed billboard into position (stick).

No other parts to mount the billboard atop the factory roof were supplied in the kit – which I thought would not produce a secure attachment or look realistic. Therefore, I made a pattern from which I fabricated four “A-frames,” as shown in Photos 58 and 59. The pattern aided in making all the “A-frames” with nearly the same angle and dimensions.


I then mounted the “A-frames” to the rear of the billboard, as shown in Photo 60. I also added a connecting cross-member and square mounting pads at the bottoms of the “A-frames.” The mounting pads were punch-outs from the laser-cut window frames.
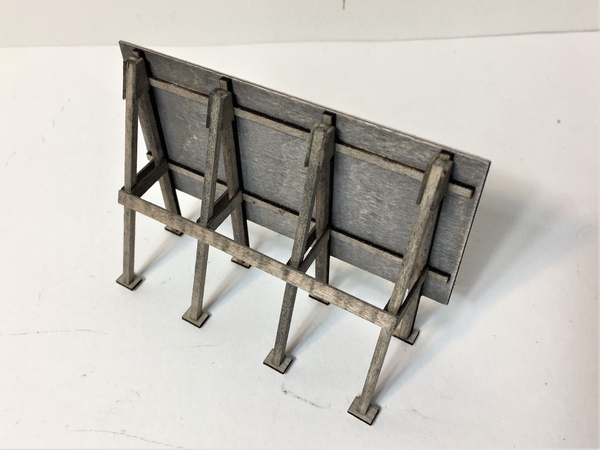
Photo 61 is a front view of the completed billboard.

The kit also included a “Witzinger’s” sign that was sized and shaped to cover the front wall of the office above the awnings and up to the peak. Too big, in my opinion. Worse yet, the lettering was of variable size. Unfortunately, I don’t have any printing capability right now, so my choices were to use the kit sign or omit it altogether. So, I cut the sign down to a smaller size but retained the lettering and glued it to a thin backing. I also cut surrounding trim pieces, painted them black, and attached them to the edges of the sign. The completed sign is shown in Photo 62.

Photos 63 and 64 show Witzinger’s with the billboard and sign in place.


The loading dock and auxiliary roof in front of the factory doors were next.
The auxiliary roof in front of the factory doors was made from a piece of basswood covered with construction paper and painted black to match the factory roof. As shown in Photo 65, I added a stiffener and three supporting brackets.

The loading dock was constructed from many small pieces, some of which are shown in Photo 66. Every loading dock part had to be cut to length individually from stripwood.
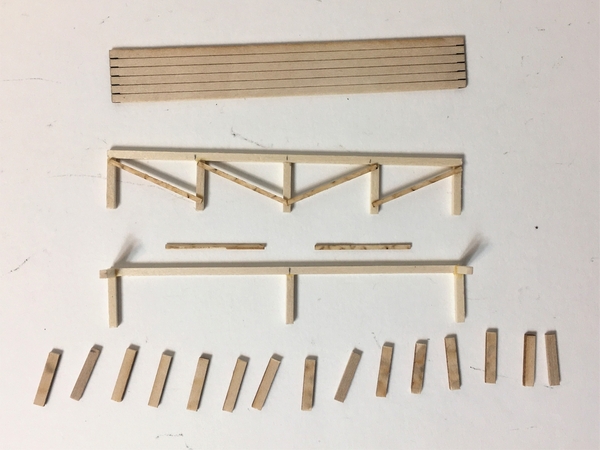
Photo 67 shows the assembled loading dock and Photo 68 shows it ready to be attached to the factory front. It took me five hours to make the loading dock.


The completed model is shown in Photos 69 through 73, and on the layout in Photo 74.






I spent eighty-five hours building Witzinger’s.
At this point, I plan to build another structure model for the layout expansion. Depending on the other models I select, and their placement on the expansion, there is a possibility that I will eventually expand Witzinger’s with an addition at the side of the factory.
MELGAR