I eliminated the stop/start cycling of my dual Pittman driven Kohs GG1 by enhancing the cooling to the PS3 circuit board. It now runs for at least 20 minutes (whereas it used to run only 2-3) and pulling more passenger cars. I have no reason to believe it could not run much longer
The enhanced cooling was accomplished with the following
- Raised the PS3 board, and opened up both the plastic carrier board and the brass mounting plate so air can flow freely underneath the board
- Added commercial finned heat sinks to the two FETs under the board and to the bridge rectifier aluminum heat sink. These were attached using Thermattach: an aluminum mesh with an adhesive applied to both side.
- Re-applied thermal paste between the factory heat sink and the bridge rectifier, and improved the thermal connection of the heat sink to the chassis
- Added twin miniature muffin fans to blow air onto the underside of the board, and specifically to the new FET heat sink. (Thanks Mario for the idea!)
Details and photos to follow, so everyone will know
HOW I DID IT…….
I built this from the bottom up, so I started with the fans. The Kohs GG1 came with twin speakers sandwiched between the chassis and the interior floor. Both are made from brass. The speakers were too small and tinny, so I chucked them and used my own speakers mounted behind the grilles on the shell.
The fans I used were from Amazon:
Operating voltage: 5V Current: 0.2 A
- Brushless DC fan
- Fan dimensions: 30mm x 30mm x 8mm
- Adafruit 4468
- UNSPSC Code 43201619
https://www.amazon.com/gp/prod...00?ie=UTF8&psc=1
Here is what one looks like:

I bored out two 1 1/8” holes for the fans in the chassis, using a hole saw and a 3/8” chuck adapter for my precision drill press:

If you look through the sawdust (which came from drilling into the underlying wood support I needed to hold this chassis) you can see the original speaker holes. Everything cleaned up rather nicely, but I painted the chassis with VHT Satin paint just so it looks nice. Here is the chassis all cleaned up with the holes for the fans in the floor. You can see where the speaker holes were, and in some places they guided my drill to a different spot than I had intended:

Here the fans have been screwed in place. They fit in the location of the original speakers (which I could not use because they were the wrong impedance and fairly poor quality):

Here is the underside view of the floor. Note I managed to keep the Kohs nameplate:

I cut a rectangular hole in the interior floor. Those cylinders are tungsten weights added for traction. You can just see the cab seats at the extreme right and left of this photo
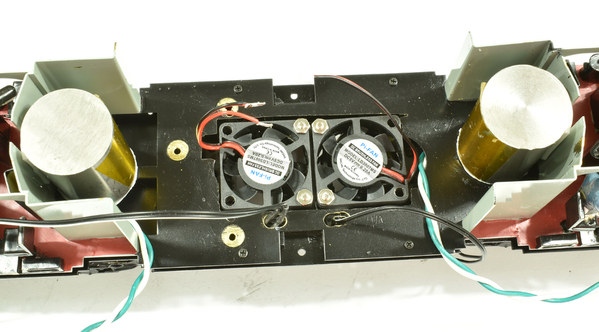
As you can tell, I ended up having to pull the outboard retaining screws for each fan, as they interfered with the truck rotation. At this point the running gear has been installed. The green and white wires go the motors, the black and white wires that protrude through the two holes just below the fans go to the electrical pickups.
The good news is the fans only stick up about 1 mm above the false floor, so I am not compromised for height.
I installed the brass mounting plate for the PS3 board on the chassis with four aluminum stand offs. The mounting plate is about 0.150” above the fans

The brass plate has been hollowed out to allow the free flow of air. I used NT-H1 Thermal Paste at both ends of the vertical standoffs, and I cleaned the paint off the chassis underneath the standoffs. Anything to encourage heat to leave the boar
In this photo the plastic carrier board has been installed on the brass mounting plate. I cut out most of the cross supports in the carrier board to encourage air flow. I later even cut out the bar at the left end, and replaced it with a .040" Phosphor Bronze wire The green and white wires are from motors, black and white from the pickups, and the red and white are for fans:

This is the underside of PS3 Board. The two large square black units, Q201 and Q 309, are the FETS which will get the heat sink

I applied Kapton tape over the components next to the FETS, so the heat sink can’t possibly short them out. It shouldn’t anyway, but no harm being sure

I used Thermattach #411 to make good contact between the FETs and the heat sinks. It is essentially an etched aluminum sheet with adhesive applied to both sides

It available from Digi Key. This is what the Thermattach looks like. In this photo one of the protective sheets has been removed, and the heat sink attached (DIGI-KEY #TGH-0220-04, Aluminum Heat Sink 22 x 22 mm). The heat sink has been trimmed to just cover the FETs and to clear the board carrier:

The Thermattach was trimmed to match the heat sink, the other protective sheet was removed, and then the heat sink attached to the FETs.

To encourage air from the fans to flow from right to left, I oriented the heat sink fins along the longitudinal axis. In the photo above you can see the aforementioned Phosphor Bronze wire in place of the left hand slat. Here is the board installed:

You can see the finned heat sink attached to the factory supplied rectifier heat sink. This side view shows the fans and the FTE heat sink right above them.

Not the most optimal aerodynamically efficient design, I’ll admit. But there should be enough airflow past the heat sinks…..
I had to install a main bus (made from two HO rails) to distribute AC power from the track:

Connections are (from left to right): harness to the number boards (they are always lit and powered by one of those John Will LED drivers), AC to the DCS board, AC to the fan driver circuits, and AC power from the track via the pickups. Obviously with this arrangement the fans are on whenever track power is applied. But I did not want to draw any more current through the PS 3 components than needed. Besides, the fans are designed to be on all the time.
This is the other side, showing the fan wiring. Note the fan rectifier is attached directly to the chassis. Not that I expect any cooling issues with only 0.4 A going through it. You can also see the buck convertor that drops the 18 Volts DC from the rectified track power down to the 5 Volts DC needed for the fans

And that’s about it.
I still need to put the shell on, but I don’t see any problems. The Kohs has real photo etched cooing vents on both sides and both ends just like the real GG1, so there should be no problem getting the hot air out. If there is, I have two additional fans I can add to extract the air.
A few more notes:
- Per my original thinking. I found two high efficiency Faulhaber motors and tried them out. The good news is they dropped the current by about 0.3 Amps. The bad news, they are substantially lighter than the Pittmans (a full 5.2 oz), so I had to add weight back to the chassis to climb an uphill curve. Which, you guessed it, caused the draw to go right back up to within a statistically insignificant range of the Pittmans.
- Readers may recall that the GG1 ran fine for several years, and only recently started this stop/start cycling. It was postulated that this may have been caused by the board going bad. The real culprit is much simpler… I reversed the directions of my Sunset GG1-pulled Congo passenger train and this Kohs GG1 pulled passenger train. Running in this new “direction” the Kohs-pulled train had to traverse an uphill super elevated curve, whereas in the original direction the uphill was shallower and straight.
- When I installed the fans I hoped they would be loud enough to give the GG1 the sound of real blowers. No such luck. They are too quiet.
- My sincere thanks to everyone who offered helpful suggestions, advice, and ideas in this thread. Most notably
- Gunrunnerjohn
- GGG
- Harmonyards
- CentralFan1976
- Engineer-Joe
With that the saga ends, and I am ready to go on to less challenging problems. Like developing a clean, plentiful, compact source of energy.