Started building the operating mechanism for the disconnecter. After printing out the drawing and sticking it to some brass sheet with 3M77, I located all the holes and drilled them while the drawings were still attached to one big piece. I then cut them out using a jeweler's saw. This went pretty well.


After cleaning up all the edges with the belt sander, files and sanding sticks, they came out decently.

Here's where things started getting dicey, before completely screwing up.
To attaching the moving rods to the bell cranks, I chose to solder 0.032" brass rod to the plates with the small holes,

then using the small spacers that I produced on the lathe from some small diameter brass tubing, I trimmed the pins to the same .052" height. I assembled the pieces together and then attempted to solder the blank up plate. My idea was to have the upper plate capture the rod onto the pin so it wouldn't fall out. Everything went swimmingly until the very last piece. I was using the resistance soldering unit to apply the heat.

And here's what it all looked like when things starting hitting the fan. First, I couldn't get the solder to behave to attach the bottom plate to the shaft. When I picked up the unit to look at it, the bottom plate along with all the rods, fell apart. Then one of the eyes on the long bar broke from the center bell crank, finally it all came apart.
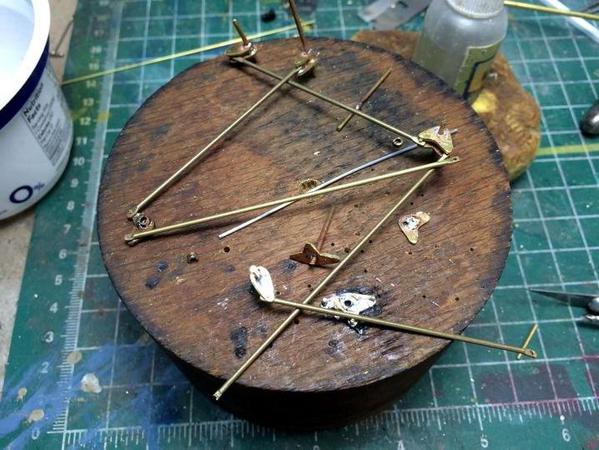
With this failure, I'm rethinking the engineering. First of all the brass is too thick. It scales out to almost 2 inches. I bought some .015" brass sheet today to remake the bell cranks. Next, soldering the pins on one side and attempting to put a blank plate on top to contain the rods wasn't good. The pins should go through both pieces. Lastly, the center large bell crank actually blocks 90º rotation. At best it gives 45º. To correct this problem I need to separate the right left rods from the fore and back rod and mounted on different planes.
So here's plan B. I'm going to solder two thicknesses of brass together, and drill and cut them at the same time to ensure that everything lines up. I will then Solder the tops and bottoms together with the spacer and center shaft, and then install the rods and pins. The pins won't need to be soldered at all. I'll just pinch the pin that extends out of each side to make it so it will no longer fit into the hole and then trim of any excess. This will allow me to do all soldering without any moving parts in the way.
If this doesn't work, plan C is to simulate the whole affair with styrene.
On another topic. I'm going on a private tour of the Heaven Hill distillery in southwest Louisville on Friday. I went on Google Earth to get some aerial pictures of this installation. It's not a very big plant and could work well with selective compression. Heaven Hill Bourbon has two installations. The distillery with some old aging houses in Louisville, and a very large barreling, aging and bottling facility in Bardstown, KY. The Bardstown bottling plant is 1,200 feet long by almost 800 feet deep. In O'scale, that's 25 feet long, by 16 feet wide, and that's just one building. So I'm staying away from that.

You can't see the storage silos in the above picture. There are 6 big ones that are about 25 feet in diameter. They could be shrunk in size and I wouldn't need 6. My trip on Friday will certainly help me in understanding what can be done in my scale and what should be left out.
This picture shows some old aging houses in Louisville. These are big. They're too big to do in scale and I'd only make one of them. They look like brick structures. In Bardstown, they're corrugated metal siding covering a very large timber structure. Building a "rick house" is an art in itself. They entirely constructed of very heavy oak timbers and the rack assembly is independent of the roof and side walls. They hold immense weight.
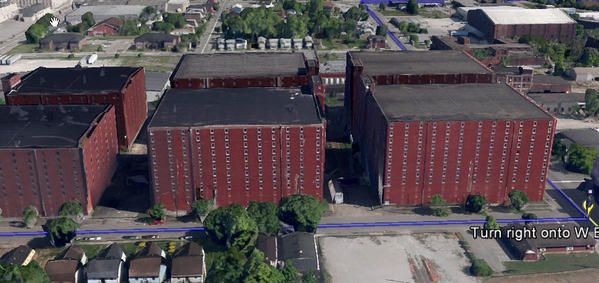
For example, a loaded bourbon barrel weighs almost 500 pounds. One rick house holds 42,000 of them. Heaven Hill has over 1,000,000 barrels in storage. 42,000 barrels weighs 21,000,000 pounds. There is plenty of air flow through the building since there is constant evaporation of alcohol vapors out of the barrel. There's no ignition sources allowed anywhere near these buildings. A 20 year-old barrel of bourbon in storage loses about half of its liquid.
Imagine trying to plan for a business where your product has to sit in inventory for 8 or more years before selling the first bottle. With bourbon undergoing an international boom (helping both Kentucky and Heaven Hill) they can't produce enough, but alcohol you distill today can't be sold for a decade or more. It's a tough business. The empty barrels cost about $42 a piece. Imagine 50 million dollars just tied up in the barrels. When they're used, they are sold to the scotch industry for aging.
I'm sure that's more information than you've asked for, but it's good for us railroaders to understand the industries on our pikes and what infrastructure they would need to thrive. Modeling any large industrial facility in O'scale is a challenge. Just ask the guys building petroleum refineries and steel mills. A bourbon distillery has lots of interest having some food industry and chemical industry aspects. They are served by railroads especially to bring in raw materials. Heaven Hill has their own tractor-trailer fleet for delivery.