Tours of Union Pacific Steam Shop to start Friday
4014 Restoration
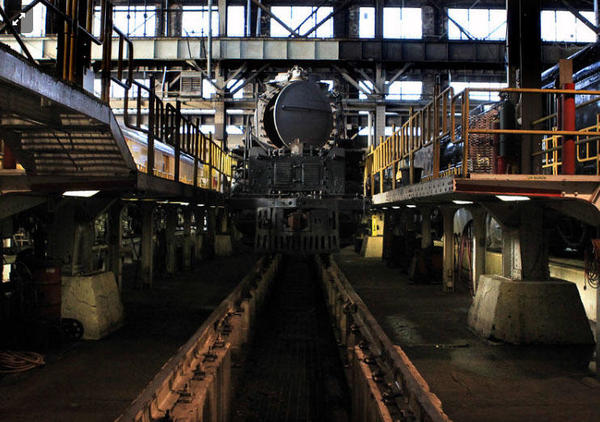
Click here for details Oct 30, 2016 from Ellen Fike, Wyoming Tribune Eagle / AP - Associated Press
Darren Rudloff was blown away when he found out visitors from Montana and Ohio had already purchased tickets for the upcoming rare tours of the Union Pacific Steam Shop.
“That really shows the strength of this attraction,” the CEO of Visit Cheyenne said. “This is such a unique opportunity for train enthusiasts to see the working steam shop and to see the renovation of the Big Boy.”
The building tours, which normally only happen once a year during Cheyenne Depot Days in May, will kick off Friday and run until late March. There won’t be tours during December, however.
Anyone who purchases a $20 ticket for the outing will get the chance to visit the Cheyenne Depot Museum, the steam shop and see the progress on the restoration of the Big Boy 4014 – a large steam engine that was built in 1941.
The Big Boy arrived in Cheyenne in 2014 with the expectation that the reconstruction would take anywhere from three to five years. However, restoration will now likely take five to seven years to complete.
“There were only 25 Big Boys originally made,” Rudloff said. “Most are in parks or museums, but this is such a unique effort to take one of these old engines that has been out of duty for so long and restore it back to working order.”
The tours, which will last two hours, start on the second floor of the Cheyenne Depot Museum, where guests will see an overview of the train yard. From there, guests will board one of the trolleys and go to the steam shop, where UP employees will give a detailed run-through of the building and show off the engines inside.
Participants will have to wear closed-toe shoes and sign a liability release before going on the tour. Hard hats will be provided.
The steam shop is a major attraction during Depot Days, which usually brings in around 5,000 visitors every year, so Rudloff said now was a perfect time to open the building up to the public, albeit for a short time.
“The large crowds show the demand to see what’s going on the steam shop,” he said. “We see visitors at the Cheyenne Depot Museum every day, wanting to see the shop and know about the Big Boy updates. We hope these tours will help satisfy that demand.”
Visit Cheyenne and Union Pacific partnered last year to do test runs of the tour, which turned out to be successes.
Rudloff expects the excursions will draw more out-of-town visitors, as well as curious residents. But, he also hopes more tours will come from the first 15 dates.
“Cheyenne is known as a railroad town,” he said. “We have some of the most amazing artifacts in the UP yards, behind closed doors. This opportunity is really special, because you can see steam engines that aren’t really around anymore. We hope to see a lot of positive response from this.”
Photo of 4014 Oct. 30, 2016 by Blain McCartney / Wyoming Tribune Eagle / AP
Gary - Railfan